Specialist Tips for Picking the Right Metal Stamping Providers for Your Demands
Specialist Tips for Picking the Right Metal Stamping Providers for Your Demands
Blog Article
Discovering the Globe of Steel Stamping: From Layout to Manufacturing
Within the realm of manufacturing, steel stamping stands out as a specific and effective approach for shaping metal sheets right into various types with remarkable uniformity. From the initial style phase where intricate patterns take shape to the complex manufacturing procedures, metal marking is a mix of virtuosity and design. Delving into this globe unveils a complex interaction of imagination and technological proficiency, supplying a glance into a world where advancement meets workmanship.
History of Steel Stamping
Steel marking, a commonly used production procedure today, has an abundant background that goes back to ancient times (Metal Stamping). The beginnings of metal stamping can be mapped to ancient people such as the Egyptians, that made use of marking strategies to embellish fashion jewelry and ornaments with elaborate designs. Over time, steel marking advanced, with human beings like the Greeks and Romans using it for producing coins and decorative items
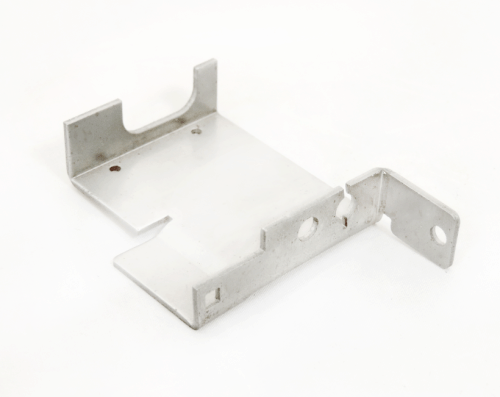
In the 20th century, steel stamping proceeded to develop with the integration of automation and computer system numerical control (CNC) modern technology. These developments further enhanced the efficiency and precision of steel stamping procedures, making it a vital part of contemporary manufacturing throughout markets such as automotive, aerospace, and electronic devices. Today, steel stamping continues to be an important production process, integrating practice with development to meet the needs of a constantly progressing industry.
Style Factors To Consider and Prototyping
When developing metal marking projects, precise focus to create factors to consider and prototyping is important for making certain optimal manufacturing results. Layout considerations in metal marking consist of material choice, component geometry, tooling design, and manufacturing usefulness. Choosing the best product is crucial as it affects the component's efficiency, price, and manufacturability. Part geometry Homepage influences the complexity of the stamping process and the performance of the last product. Tooling layout plays a substantial role in the success of metal stamping projects, impacting part accuracy, tool durability, and manufacturing effectiveness.
Prototyping is a vital phase in the metal stamping procedure that permits engineers to test the layout, confirm manufacturability, and make essential changes prior to full-blown production. Prototyping assists identify potential issues early on, conserving time and prices in the lengthy run. It likewise offers an opportunity to optimize the layout for performance and top quality. By carefully taking into consideration layout elements and using prototyping, manufacturers can simplify the steel stamping procedure and accomplish high-grade, cost-efficient production outcomes.
Tooling and Devices Essentials
Considering the vital function that tooling style plays in the success of metal stamping projects, understanding the vital tools and devices required is critical for achieving effective production outcomes. Fixtures hold the steel in area throughout the marking process, guaranteeing accuracy and repeatability. Spending in high-grade tooling and tools not just enhances production efficiency yet additionally leads to greater precision, reduced waste, and total price financial savings in steel stamping operations.
Manufacturing Refine and Quality Assurance
Successfully managing the manufacturing process and carrying out robust Go Here quality control actions are vital for ensuring the success of metal marking projects. The production procedure in metal stamping entails a series of steps that need to be carefully collaborated to attain optimal results.
Quality control in steel stamping is critical to deliver items that fulfill the needed specs. By maintaining stringent top quality control criteria, makers can support their credibility for delivering high-grade steel stamped products.
Applications and Sector Insights
In the world of metal marking, the effective application of production procedures and top quality control steps directly affects the effectiveness and reliability of numerous market applications and provides useful insights into the market's functional dynamics. Metal stamping locates extensive application across varied markets, including auto, aerospace, electronics, and devices. In the vehicle sector, steel stamping plays a crucial function in producing elements such as chassis, brackets, and architectural get rid of high accuracy and efficiency. The aerospace sector relies upon steel stamping for producing detailed parts like panels, braces, and fittings that satisfy rigorous high quality criteria (Metal Stamping). In the electronics market, steel stamping is utilized to develop precise elements like adapters, terminals, and heat sinks. In addition, steel stamping assists in the manufacturing of various family devices, including refrigerators, cleaning machines, and ovens, by supplying cost-efficient solutions for producing sturdy and complex parts. Comprehending the applications and market understandings of metal stamping is important for optimizing production processes and improving item top quality throughout various sectors.
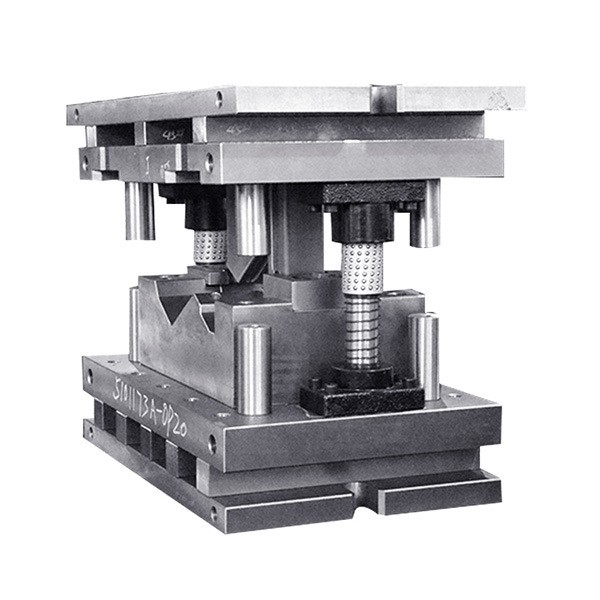
Conclusion
Style factors to consider, prototyping, tooling, devices, production processes, and quality control are essential elements of metal stamping. With its prevalent applications and market understandings, metal marking visit continues to be a flexible and reliable manufacturing procedure.
Report this page